Using the calculator, we find that the percentage of the first manufacturing order (5) relative to the total quantity of both orders (15) is (33.333%).
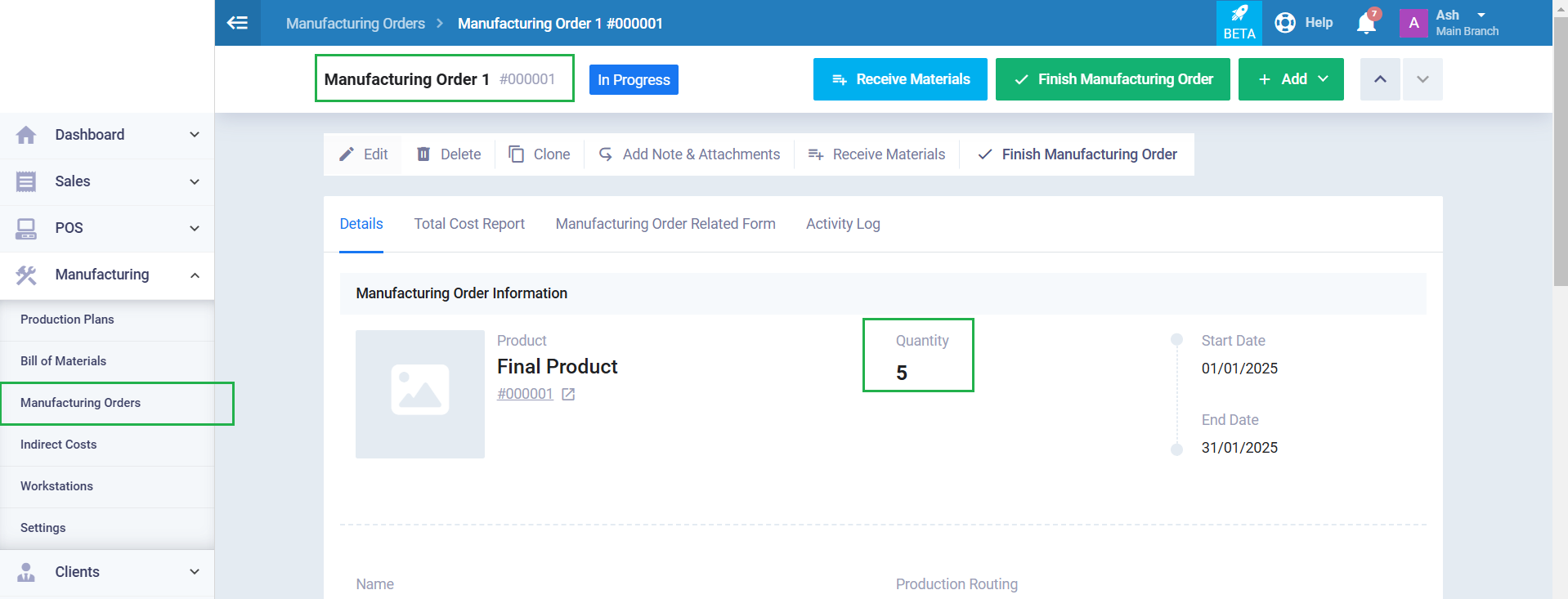
The amount of indirect cost (the entry) to be allocated to both orders is 1,000. When calculating the share for the first manufacturing order based on its percentage, which is 33.333%, we find the amount to be 333.333, as it automatically appears next to this manufacturing order in the “Indirect Cost” page.
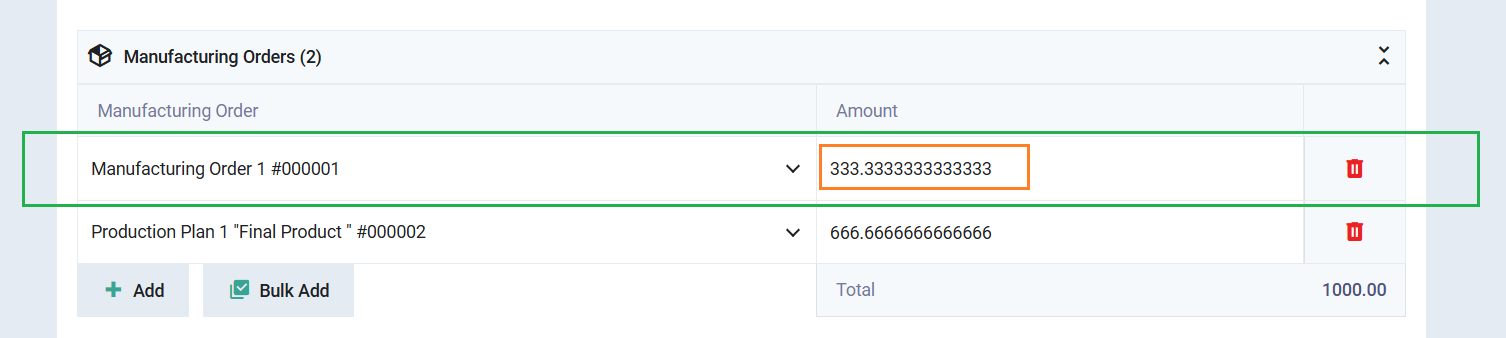
Using the calculator, we find that the percentage of the second manufacturing order (10) relative to the total quantity of both orders (15) is (66.6667%).
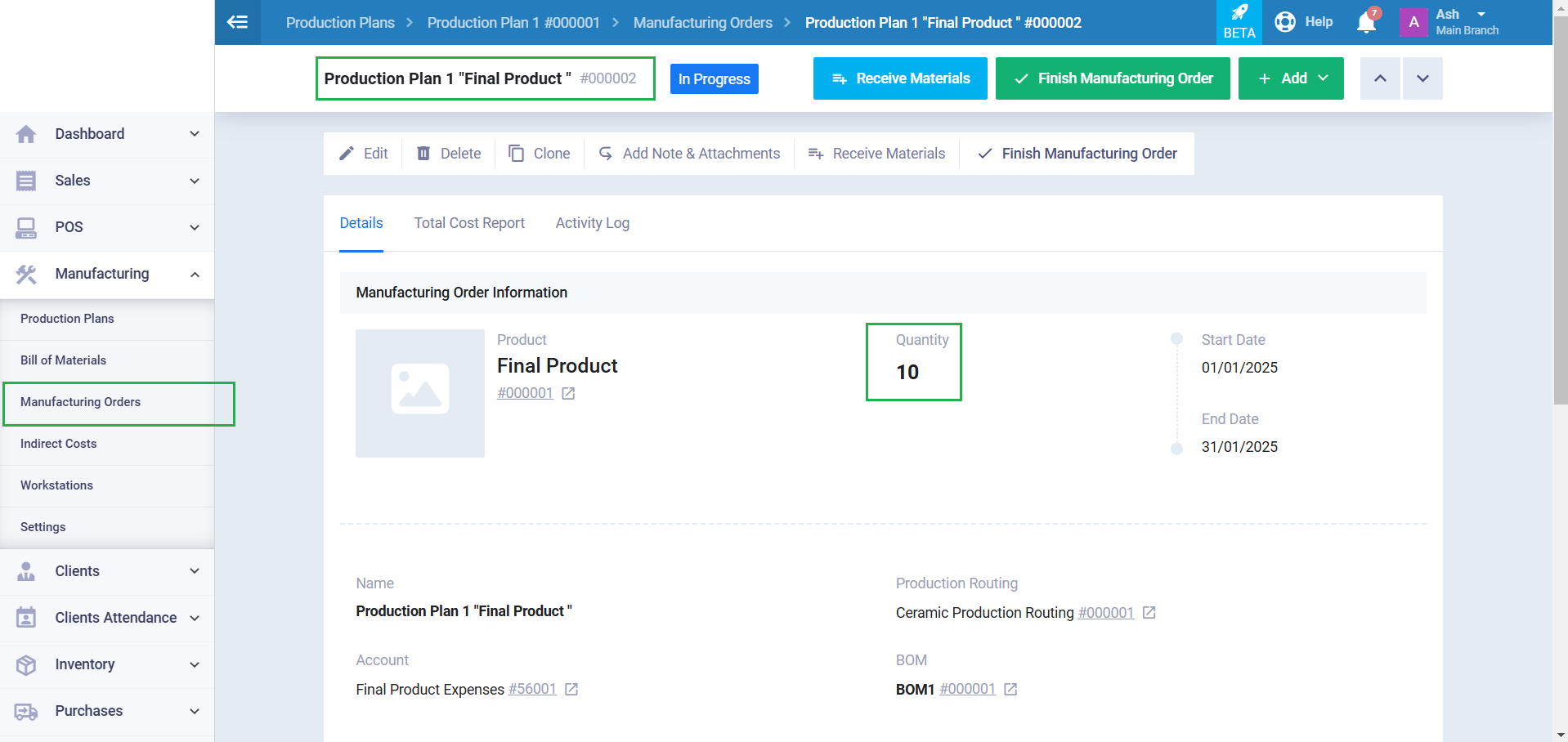
The amount of indirect cost (the entry) to be allocated to both orders is 1,000. When calculating the share for the second manufacturing order based on its percentage, which is 66.6667%, we find the amount to be 666.666666, as it automatically appears next to this manufacturing order in the “Indirect Cost” page.
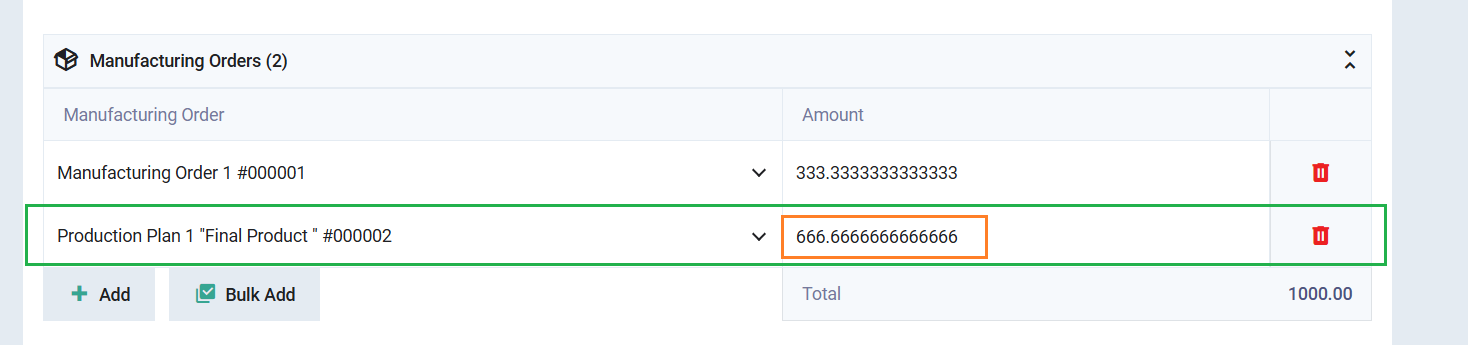
The same principle is applied when selecting the “Based on Amount” distribution type, replacing the quantity of the final product with the actual cost of the manufacturing order.